
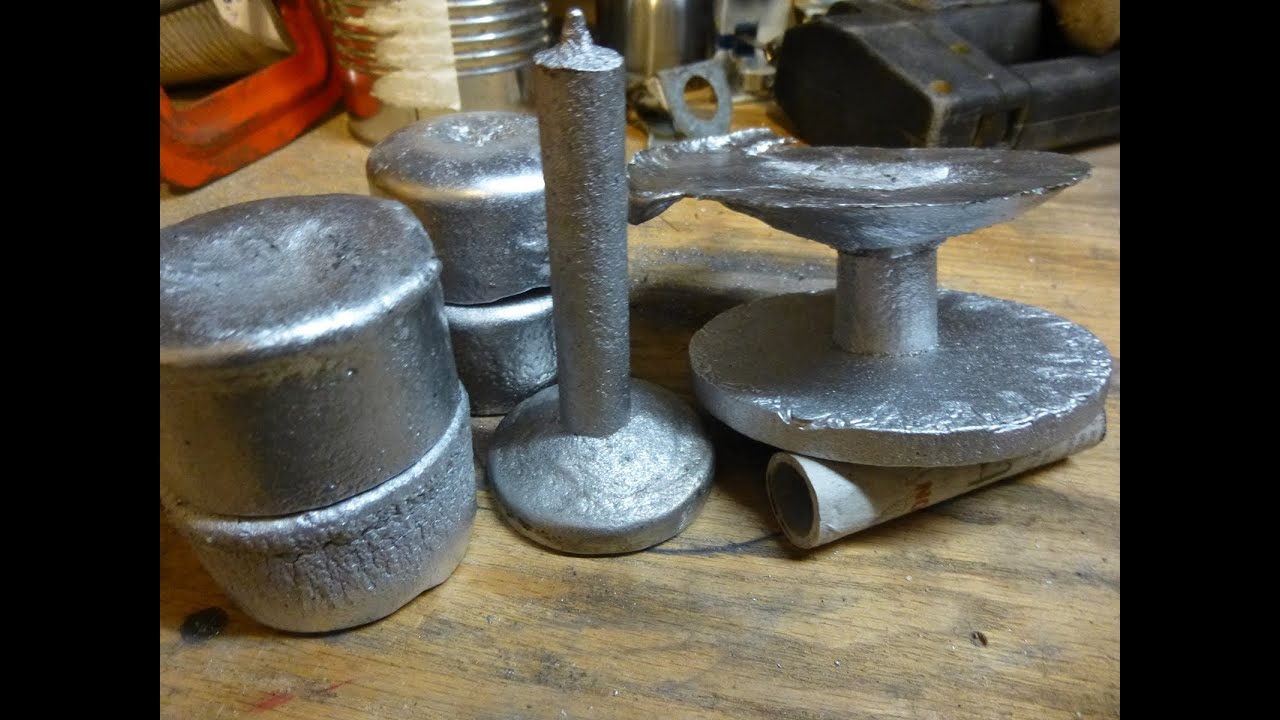
#Lost foam casting plaster iso#
Sinotech has audited, qualified and worked with QS-9000 and ISO certified lost foam factories in China, Taiwan and Korea for over 12 years. Sinotech can ensure excellent lost foam castings from China, Taiwan and Korea and is very price competitive. The finished results from Lost Foam Casting can be greatly improved with the additional use of plaster feeders and vents. Types of parts that can be made using these processes are pump housings, manifolds, and auto brake components. Lost Foam Casting: Plaster Feeders and Vents Making Plaster Feeders and Vents to Improve the Casting Process. Foam components can be glued together in stack to allow undercuts and.
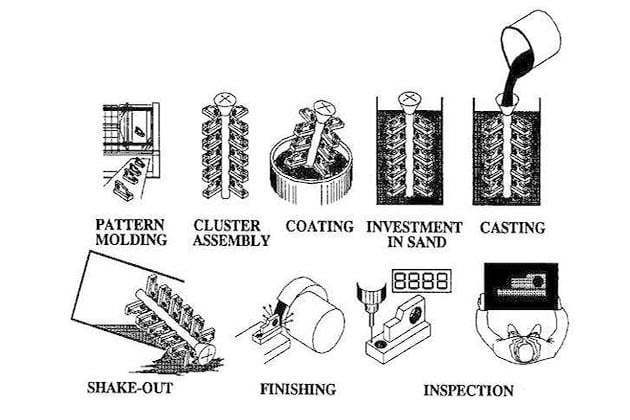
Typical materials that can be cast with this process are aluminum, iron, steels, nickel alloys, copper alloys. First, components are molded in expanded polystyrene foam. Artisans create an impression of a non-wax model by placing it inside a hard gated outer mold. Size limits are from 400 g (1 lb) to several tons. This item may consist of stone, metal, wood, plaster or clay. Surface finish can be held from 2.5mm to 25mm (0.1in to 1.0 in) rms. Minimum wall thicknesses are 2.5 mm, tolerances can be held to. Figure 11.13 Schematic illustration of investment casting (lost-wax) process. However, the pattern cost can be high due to the expendable nature of the pattern. dimensional tolerances few or no finishing operations. In this process, the pattern is made of polystyrene foam, which the sand is packed around, leaving the foam in place. This can make complex shaped castings without any draft or flash. Lost Foam Process Starting in the early 1980s, some metal castings such as automotive engine blocks have been made using a sand casting technique conceptually similar to the lost wax process, known as the lost foam process. As the metal is poured, the foam vaporizes, and the metal takes its place. Plaster mold casting is a metalworking casting process similar to sand casting except the molding material is plaster of Paris instead of sand. Investment casting uses a wax pattern coated with a. The pattern is encased in a one-piece sand mold. The methods to produce gray iron castings include lost foam, mold, and sand casting. The foam pattern is coated with a refractory material.

Lost form (full-mold casting) is a technique similar to investment casting, but instead of wax as the expendable material, polystyrene foam is used as the pattern. These processes consist of die casting, permanent mold casting, sand casting (green sand and dry sand), plaster casting, investment casting, and continuous.
